ABB PM511V08 3BSE01180R1 CPUProcessor module
(1) The temperature PLC requires the ambient temperature to be 0~55oC. During installation, it should not be placed under the elements with large heat, and the space for ventilation and heat dissipation around should be large enough.
(2) Humidity To ensure the insulation performance of PLC, the relative humidity of air should be less than 85% (no condensation).
(3) The vibration shall keep the PLC away from strong vibration sources and prevent frequent or continuous vibration with vibration frequency of 10~55Hz. When vibration is unavoidable in the use environment, damping measures must be taken, such as damping rubber.
(4) The air shall be free from corrosive and flammable gases, such as hydrogen chloride, hydrogen sulfide, etc. For the environment with more dust or corrosive gas in the air, PLC can be installed in the control room or control cabinet with good sealing.
(5) The power supply PLC has certain ability to the interference caused by the power line. In the environment with high reliability requirements or serious power interference, an isolation transformer with shielding layer can be installed to reduce the interference between the equipment and the ground. Generally, PLC has DC 24V output to the input end. When the input end uses external DC power supply, DC stabilized power supply should be selected. Because of the influence of ripple, the common rectifier filter power supply is easy to make the PLC receive error information.
2. Interference in control system and its source
On-site electromagnetic interference is one of the common factors that can easily affect the reliability of the PLC control system. It is called to solve the problem first, find out the problem, and then propose solutions to the problem. Therefore, the source of on-site interference must be known.
(1) Interference sources and general classification
Most of the interference sources that affect the PLC control system are generated at the position where the current or voltage changes sharply. The reason is that the current changes to generate magnetic field, which generates electromagnetic radiation to the equipment; The magnetic field changes to generate current, and the electromagnetic wave is generated at high speed. Generally, electromagnetic interference is divided into common mode interference and differential mode interference according to different interference modes. Common mode interference is the potential difference between the signal and the ground, which is mainly formed by the superposition of the power grid connection, the ground potential difference and the common state (in the same direction) voltage induced by space electromagnetic radiation on the signal line. Common mode voltage can be converted into differential mode voltage through asymmetric circuit, which directly affects the measurement and control signal and causes component damage (this is the main reason for the high damage rate of I/O modules in some systems). This common mode interference can be DC or AC. Differential mode interference refers to the interference voltage acting on the two poles of the signal, which is mainly formed by the coupling induction of the space electromagnetic field between the signals and the conversion of the common mode interference by the unbalanced circuit. This interference is superimposed on the signal and directly affects the measurement and control accuracy.
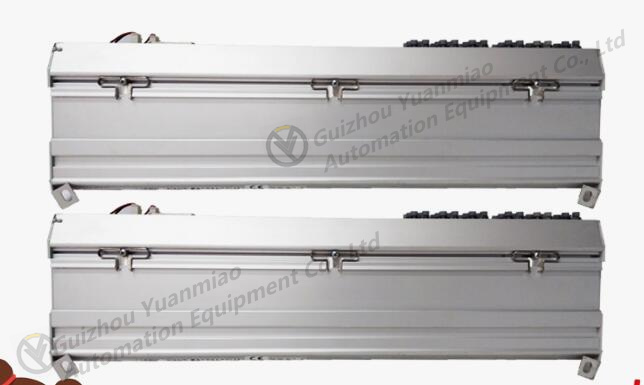
(2) Main sources and ways of interference in PLC system
A. Strong current interference
The normal power supply of PLC system is supplied by the power grid. Due to the wide coverage of the power grid, it will be subject to all spatial electromagnetic interference and induce voltage on the line. In particular, changes in the power grid, surges in knife switch operation, starting and stopping of large power equipment, harmonics caused by AC and DC drives, and transient impact of short circuit in the power grid are all transmitted to the power source through transmission lines.
B. Interference in cabinet
High-voltage electrical appliances in the control cabinet, large inductive loads, and disordered wiring are easy to cause a certain degree of interference to the PLC.
C. Interference from signal line
All kinds of signal transmission lines connected with the PLC control system, in addition to transmitting various kinds of effective information, will always be invaded by external interference signals. There are two main ways of this interference: one is the power grid interference connected in series by the transmitter power supply or the power supply of the shared signal instrument, which is often ignored; The second is that the signal line is interfered by the induction of space electromagnetic radiation, that is, the external induction interference on the signal line, which is very serious. The interference introduced by the signal will cause the I/O signal to work abnormally and the measurement accuracy will be greatly reduced, and in serious cases will cause damage to the components.
D. Interference from grounding system in disorder
Grounding is one of the effective means to improve the electromagnetic compatibility (EMC) of electronic equipment. Correct grounding can not only suppress the influence of electromagnetic interference, but also suppress the outward interference of equipment; On the contrary, the wrong grounding will introduce serious interference signals and make the PLC system unable to work normally.
E. Interference from the PLC system
It is mainly generated by the mutual electromagnetic radiation between components and circuits in the system, such as the mutual radiation of logic circuits and their influence on analog circuits, the mutual influence between analog and logic circuits and the mutual mismatch between components.
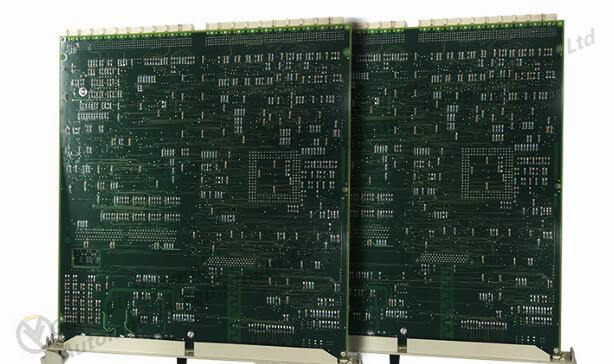
Main products: DCS system parts, robot system parts, large servo system parts of Bentley, Invensys, Woodward, Foxboro, Westinghouse, Ryan, Schneider Modicon, ABB, AB, Siemens, Motorola, GE Fanuc, Yaskawa, Bosch Rexroth, ACSO, YOKOGAWA Yokogawa, Rexroth and other major brands
ABB | 3BHB003154R0101 |
ABB | 3BHB003688R0001 |
ABB | 3BHB003688R0101 |
ABB | 3BHB003689 |
ABB | 3BHB004027R0101 |
ABB | 3BHB005171R0101 |
ABB | 3BHB005243R0105 |
ABB | 3BHE009681R0101 |
ABB | 3BHE021951R0124 |
ABB | 3BHE024747R0101 |
ABB | 3BHE027632R0101 |
ABB | 3BHE039203R0101 |
[Disclaimer]
Our company sells new products and discontinued products, and purchases such special products through independent channels. Guizhou Yuanmiao Automation Equipment Co., Ltd. is not an authorized distributor, distributor or representative of the featured products of this website. All product names/product images, trademarks, brands and microlabels used on this website are the property of their respective owners. Product descriptions, descriptions or sales with these name images, trademarks, brands and logos are for identification purposes only and do not represent any association or authorization with any right holders.